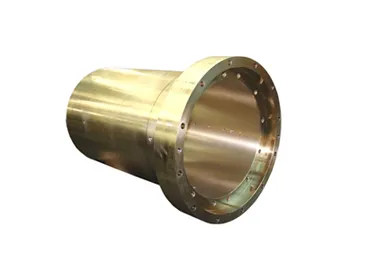
- Introduction:
Being the leading manufacturer, exporter, supplier, and manufacturer of aluminum bronze casting in India, we have gained recognition in this regard. The non-sparking and corrosion-resistant properties of aluminum bronze make it perfect for environmentally demanding applications where there is a significant risk of fire or explosion. Aluminum bronze is widely used in the mining, oil and gas, aerospace, and petrochemical industries.
Aluminum bronze casting involves the use of aluminum bronze, a type of non-ferrous alloy, in the casting process. Aluminum bronze is a copper-based alloy containing aluminum as the primary alloying element, along with other elements such as iron, nickel, manganese, and sometimes zinc.
Here are some key aspects of aluminum bronze casting:
- Alloy Composition: Aluminum bronze alloys typically contain around 6-12% aluminum by weight, along with varying amounts of copper and other alloying elements. The addition of aluminum to copper imparts several desirable properties to the alloy, including high strength, corrosion resistance, and wear resistance.
- Casting Methods: Aluminum bronze casting can be carried out using various casting methods, including sand casting, investment casting, and centrifugal casting. The choice of casting method depends on factors such as the complexity of the component, required production volume, and desired properties of the final product.
- Sand Casting: Sand casting is a widely used method for producing aluminum bronze castings, particularly for larger and more complex components. It involves creating a mold cavity by compacting sand around a pattern, then pouring molten aluminum bronze into the mold and allowing it to solidify. Sand casting offers flexibility, cost-effectiveness, and the ability to produce large components with relatively low tooling costs.
- Investment Casting: Investment casting, also known as lost-wax casting, is a precision casting method used for producing intricate and high-quality aluminum bronze components. It involves creating a wax pattern of the desired part, coating it with a ceramic shell, then melting out the wax to leave a hollow mold cavity. Molten aluminum bronze is then poured into the cavity, and after solidification, the ceramic shell is broken away to reveal the finished casting. Investment casting is ideal for producing parts with complex geometries and tight tolerances.
- Centrifugal Casting: Centrifugal casting is a method used to produce cylindrical aluminum bronze components such as tubes, pipes, and rings. It involves pouring molten metal into a rotating mold, where centrifugal force distributes the metal evenly along the mold cavity walls, resulting in a uniform casting with excellent grain structure and mechanical properties.
- Finishing Operations: After casting, aluminum bronze components may undergo various finishing operations such as machining, grinding, polishing, and surface treatment to achieve final dimensions, surface finish, and desired properties.
Overall, aluminum bronze casting offers versatility, durability, and the ability to produce high-quality components with excellent mechanical properties for demanding applications across various industries.